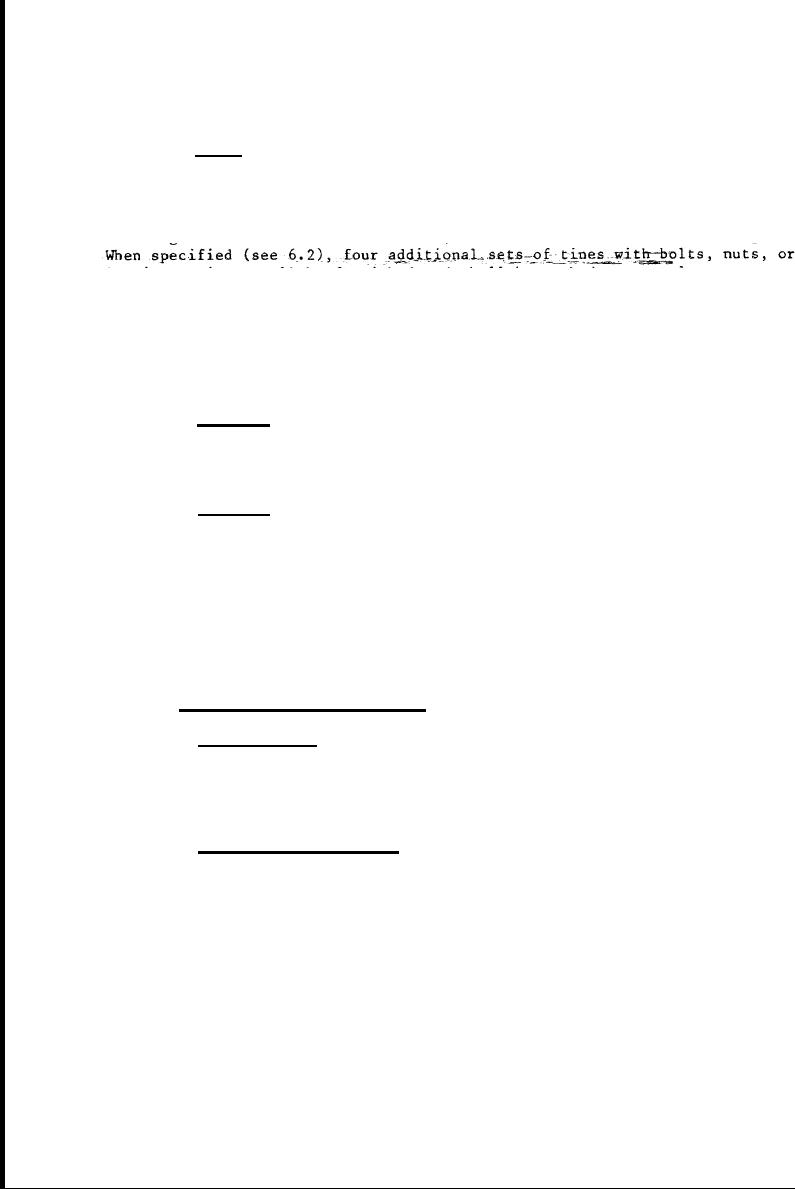
MIL-M-13081F
3.12.1 Tines. The mixer shall be equipped with one set of tines installed on
the rotor and one set of tines stored in the toolbox. The tines shall be
attached to the rotor assembly by bolts, quick release positive locking devices
or tines with wedge-shaped shanks that are knock in/knock out of forged type
sockets. All tines furnished shall be the contractor's standard mixing and
blinding tines for smooth bottom cuts, and all tines shall be interchangeable.
locking devices shall..be furnished and shall be packed separately.
3.12.2 Hood. The rotor assembly shall be enclosed in a hood that forms a
chamber to in mixing and processing the pulverized material. The hood shall
be made of steel not less than 0.1345 inch (3.4163 mm) nominal thickness. The
trailing edge of the hood shall be hinged and operated hydraulically. The
bottom of the hood ends shall have replaceable wearing surfaces.
3.12.3 Controls. The mixer shall be furnished with a power-driven hydraulic
system to raise and lower the rotor and hood assembly and to open and close the
tailboard. All controls for the hydraulic system shall be accessible from the
operator's station in accordance with 3.5.
3.12.4 Spraybar. The mixer shall be equipped with a spraybar located so that
liquified additives will be applied as the material is blended. The discharge
angle of the spraybar shall be adjustable to permit directing the additives into
the mixing chamber. The spraybar shall be equipped with nozzles that have a
total capacity of not less than 175 gallons per minute (gpm) (662 litres per
minute). The rate of discharge shall be adjustable for any rate between 40 gpm
and 175 gpm (151 lpm and 662 lpm). The nozzles shall be attached by pipe
threads. A hydraulically actuated quick-acting-type shutoff shall be provided
for the spraybar, and provisions shall be made to stop the flow of material from
each nozzle independently, when required.
3.13 pump and metering equipment.
3.13.1 Additive pump. The mixer shall be equipped with an additive pumping
system. The pumping system shall deliver liquid asphaltic materials, asphaltic
emulsions, or-water to the spraybar at the rate specified in 3.12.4. The pump
shall be driven by a separate engine or through a hydraulic drive. All controls
for the pumping system shall be accessible from the operator's station.
3.13.2 Additive pump fittings. The pump shall be equipped with a shutoff
valve, a flowmeter valve, a flowmeter indicating the rate of discharge in
gallons per minute, and a volumeter that shall record the total gallons. A
strainer shall be provided in the inlet to the pump. The pump inlet shall be
fitted with a 16-foot length of 3-inch inside diameter rubber hose. The hose
shall be wire reinforced and shall withstand pumping asphaltic materials at a
temperature of 200 °F (93.3 °C). The pump inlet shall be equipped with fittings
end components for a 3-inch quick-disconnect coupling. Each end of the hose
shall be equipped with hose end components for 3-inch quick-disconnecting
couplings. A dust cap shall be provided for the inlet to the pump and for each
end of the hose. Each dust cap shall be secured by a chain. Provision shall be
9
For Parts Inquires call Parts Hangar, Inc (727) 493-0744
© Copyright 2015 Integrated Publishing, Inc.
A Service Disabled Veteran Owned Small Business